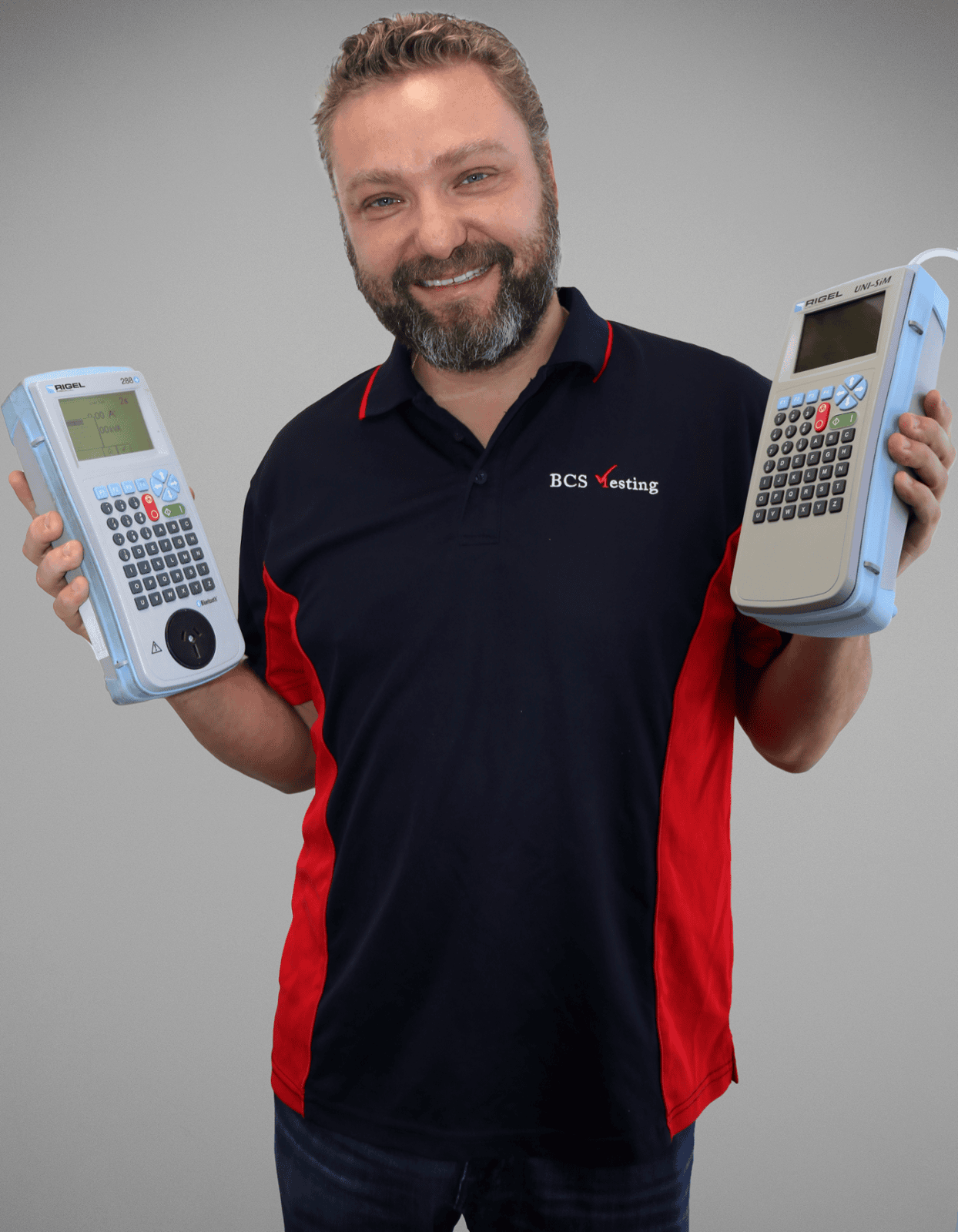
In the vast expanse of Australia, Ryan, a dedicated technician at BCS Testing, embarks on a journey that goes beyond the ordinary. From the buzzing cities to the remote outback, his mission is to ensure the reliability of medical devices through meticulous testing and tagging. A typical day for Ryan involves careful preparation, rigorous testing procedures, and overcoming unique challenges presented by the diverse landscapes he encounters.
Behind the scenes, professionals like him play a crucial role in ensuring the reliability and safety of medical devices across diverse locations in Australia. In this interview, Ryan shares his journey into the field, the technical complexities of his work, and the unique challenges he faces on a daily basis. Check it out now:
"Can you share a bit about your background and how you became involved in the field of testing and tagging?"
Hey there, readers!
Let me take you on a quick journey from the world of culinary arts to the intriguing realm of testing and tagging. I spent 23 years as a chef, crafting dishes around the globe—from the UK and Hong Kong to Australia.
Craving new challenges, I shifted gears a few years ago, earning a diploma in Building Design and Architecture. This led me to a role at a CNC laser systems company, where I initially dove into CAD-based design. However, the allure of sitting in front of a computer all day faded fast.
Hungry for hands-on experiences, I delved into courses on testing and tagging, truck driving, forklift licenses, and more during my days off. This diverse skill set paved the way for a side gig, running a company in my spare time.
Always fueled by a passion for travel and the freedom of independent work, my path took an unexpected turn when I stumbled upon a job ad for BCS Testing. I reached out to Naomi, expressing my enthusiasm, and convinced them I was the ideal candidate.
Now, I'm navigating a career that blends travel, independent work, and continuous learning. Testing and tagging may seem worlds away from the bustling kitchens I once thrived in, but it's proof that embracing change can lead to unexpected and fulfilling opportunities. Who knew a culinary journey could pave the way for such a diverse career? The adventure continues, and I'm eager to see where it takes me next.
"What does a typical day in the life of a BCS Testing technician look like?"
Well, truth be told, there's no such thing as typical in this job. Every day throws something new my way.
For instance, if it's a day filled with physiotherapy clinics, I'm bouncing between 5-6 different places, dealing with equipment in various spots. On the flip side, if it’s a large Medical Centre, my day revolves around doctors and nurses treating patients. The challenges shift with the setting, making each day unique.
"How do you prepare for your journeys across Australia, considering the vast and varied locations you visit?"
Thankfully, BCS has me covered with the right tools for safe and convenient long-distance travel.
I keep things organized with lists detailing the equipment and essentials I need. Since my trips often span many months, thorough preparation is key. It all boils down to the timeless mantra of the 3 P's: Preparation, Preparation, Preparation. It's that simple!
"Can you walk us through the technical aspects of your testing process, especially in relation to medical devices?"
Let's dive into the technical aspects of our testing process, focusing on a specific example—the Cardioline ECG. The tests we conduct on equipment are diverse, but I'll walk you through this one.
First things first, a visual check for any cable or connection damage is standard practice. Once confirmed that everything looks good, we connect our tester to the mains power. Entering the ECG AU/NZ3551 test, we proceed with the electronic test.
After the initial test, we plug the ECG leads into our patient simulator, conducting a comprehensive ECG test that includes pulse, heart rate, and waveform analysis. Running this for a few minutes ensures the machine is in top-notch condition. If everything checks out, we input the data into our tester note, print out the tag, and affix it to the machine and its power cable.
However, if we encounter a fault, it's not a roadblock. We can either organize a replacement part or set up a service at our Sydney office. Flexibility and problem-solving are key in ensuring efficient and effective testing processes for medical devices.
"What challenges do you face while conducting tests in remote areas, and how do you overcome them?"
Conducting tests in remote areas comes with its fair share of challenges, ranging from basic hurdles like a scarcity of power points to more complex issues like limited personnel on-site. How do I tackle these challenges? Well, it all boils down to one word: flexibility.
Flexibility is my ally in adapting to the unfolding situations in these remote locations. The key is to be attuned to the people and equipment at hand. Being punctual and ensuring I have all the necessary equipment on time are the first and most straightforward steps. When it comes to remote testing, flexibility isn't just a strategy; it's a way of overcoming challenges and ensuring a smooth process.
"Could you share a memorable experience from your travels that highlights the importance of your work?"
One memorable experience from my travels this year involved fixing a treadmill in a cardiologist's office in Brisbane. The unique aspect was that I had the chance to delve into researching the product, understanding what it needed for repair—a task I surprisingly found enjoyable.
The significance? The customer didn't have to endure the wait for someone to fly in and fix their machine. Both our team and the customer appreciated the efficiency. Throughout the year, similar opportunities arose, where I could help repair small pieces of equipment, enabling customers to start using them promptly. These moments underscore the tangible impact of our work on the ground.
"How has technology evolved in your field, and how does it impact your testing methods?"
As someone relatively new to the field, I've been fortunate to work with the latest and greatest testing equipment. The tools at my disposal are top-notch, significantly easing the testing process. Looking ahead to the next year, the advancements continue.
A game-changer is the implementation of unique asset IDs with barcodes for each tested item this year. Now, when revisiting a location, I can simply scan the barcode, automatically populating all the necessary information for a new test. No need to hunt down serial numbers—it's a fantastic evolution that enhances efficiency in our testing methods.
"What measures do you take to ensure accuracy and reliability in your testing procedures?"
Ensuring accuracy and reliability in our testing procedures is paramount. Our testing equipment, being brand new and state-of-the-art this year, undergoes meticulous calibration by the manufacturer. To guarantee its accuracy daily, I kick off each morning by running a simple test on a known-to-be-perfect cable. This routine check ensures that the tester remains consistent, leaving no room for deviations in our testing procedures.
"How do you build relationships with customers, especially considering the diverse locations you serve?"
Establishing strong relationships with customers across diverse locations is a key aspect of my role. Understanding the importance of efficiency and quality, I consistently brainstorm ways to streamline interactions and make the process as smooth as possible for clients.
Being naturally friendly plays a significant role. I find it easy to connect with everyone, and my broad range of interests allows me to engage with people from various backgrounds. This approach not only fosters positive relationships but also ensures that our interactions are pleasant and effective, reflecting the commitment to both quality work and customer satisfaction.
"What motivates you the most in your role as a BCS Testing technician?"
What drives me most in my role as a BCS Testing technician is the perfect blend of travel, diverse challenges, and the profound impact of our work. The sheer variety of challenges keeps me on my toes, making every day unique and exciting.
But what truly motivates me is the realization that some communities and centers heavily rely on our services. The ability to test, repair, and calibrate medical devices ensures that even the most remote areas in Australia have access to reliable healthcare. It's a crucial service for some of our nation's most vulnerable and knowing that I play a part in making this happen is incredibly rewarding.
On a personal note, getting paid to be out there, working, and connecting with people from all walks of life adds an extra layer of awesomeness to the job. It's a motivation that goes beyond the paycheck—knowing I contribute to something meaningful and impactful keeps me eager to hit the road each day.
We hope you enjoyed getting to know a bit more about Ryan. If you prioritize safety and compliance in your practice, trust BCS Testing to be your partner in this journey. Our expert technicians are ready to bring precision and reliability to your doorstep. Schedule your Test and Tag Service today and experience the assurance that comes with a commitment to quality. Your safety is our priority, always.